The most polluting industry in the world.
The construction industry generates more than 1/3 of global waste and over 40% of the world’s CO2 emissions (BBC).
Concrete and steel production themselves account for 15% of global emissions.
Additionally, construction costs have risen by 23% in 2021 alone, making people’s dreams of owning an affordable and sustainable home increasingly out of reach.
This isn’t just numbers…
It’s our forests turned into landfills, skies filled with smog, and families being priced out of the market.
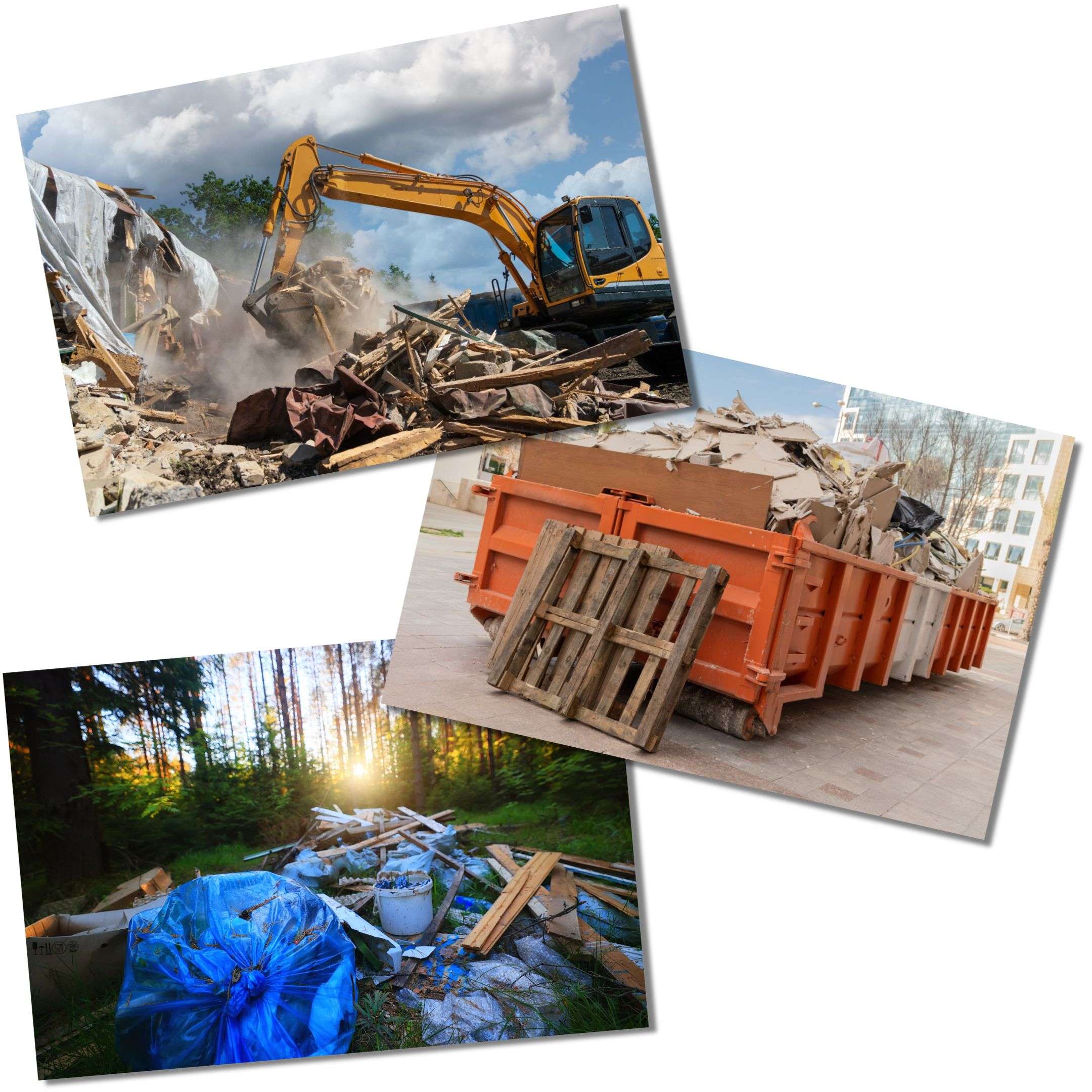
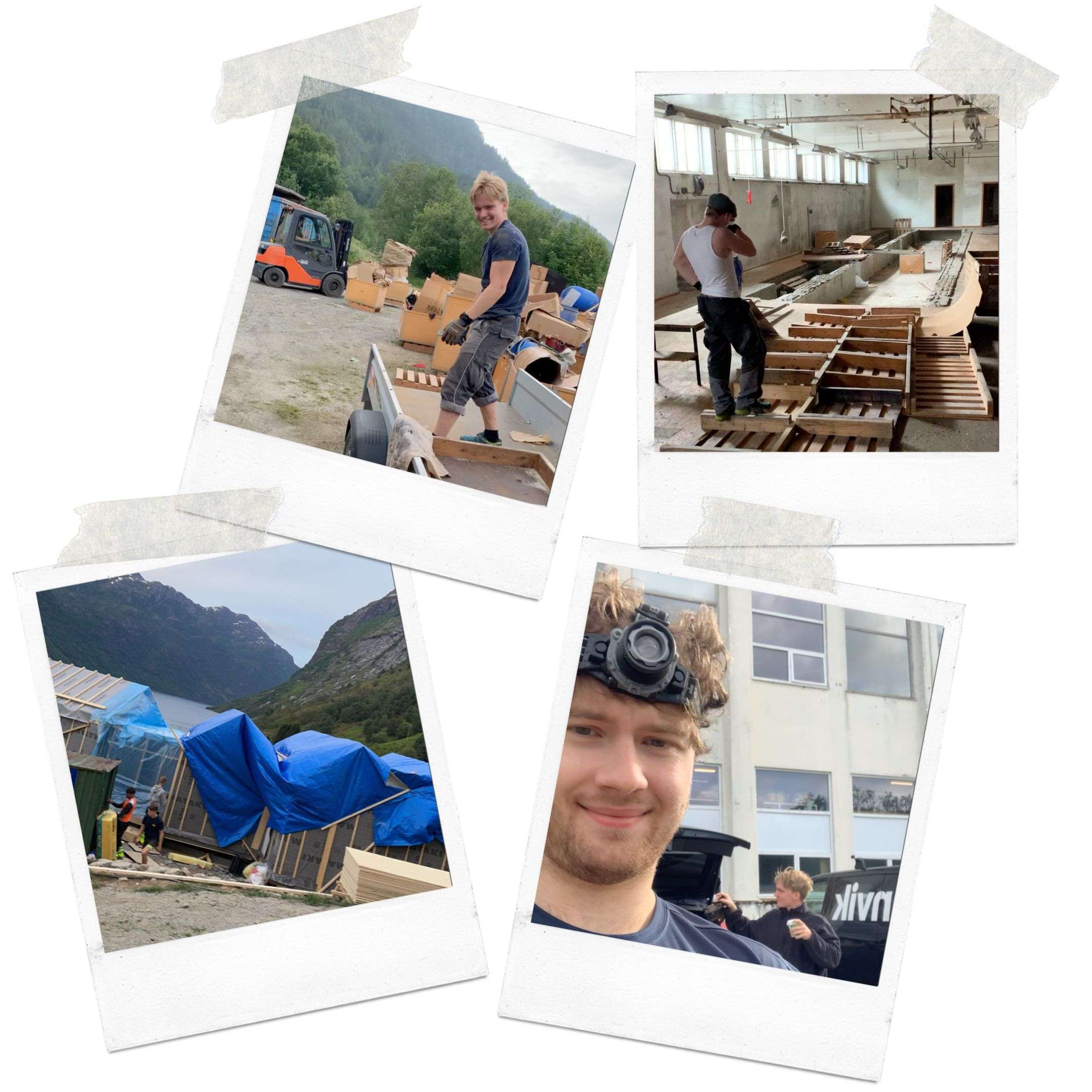
Our sustainability journey.
Our story began in 2021, among the Norwegian fjords and a few challenging construction and demolition sites.
We faced the harsh realities of traditional building: it’s tough as shit, expensive, and produces an absurd amount of waste.
These experiences motivated us to develop ways to reduce costs, waste and the burden on workers.
We discovered a solution: converting material waste into cheap, durable, and maintenance-free building materials.
“Our mission is to make building affordable and sustainable.”
The Solution-in-progress
1. We use 100% recycled materials.
We use “waste” materials in our products. Our components are fully recycled materials, such as plastics and composites from boats and wind turbines. This reduces waste, lowers CO2 emissions, and promotes sustainable building.
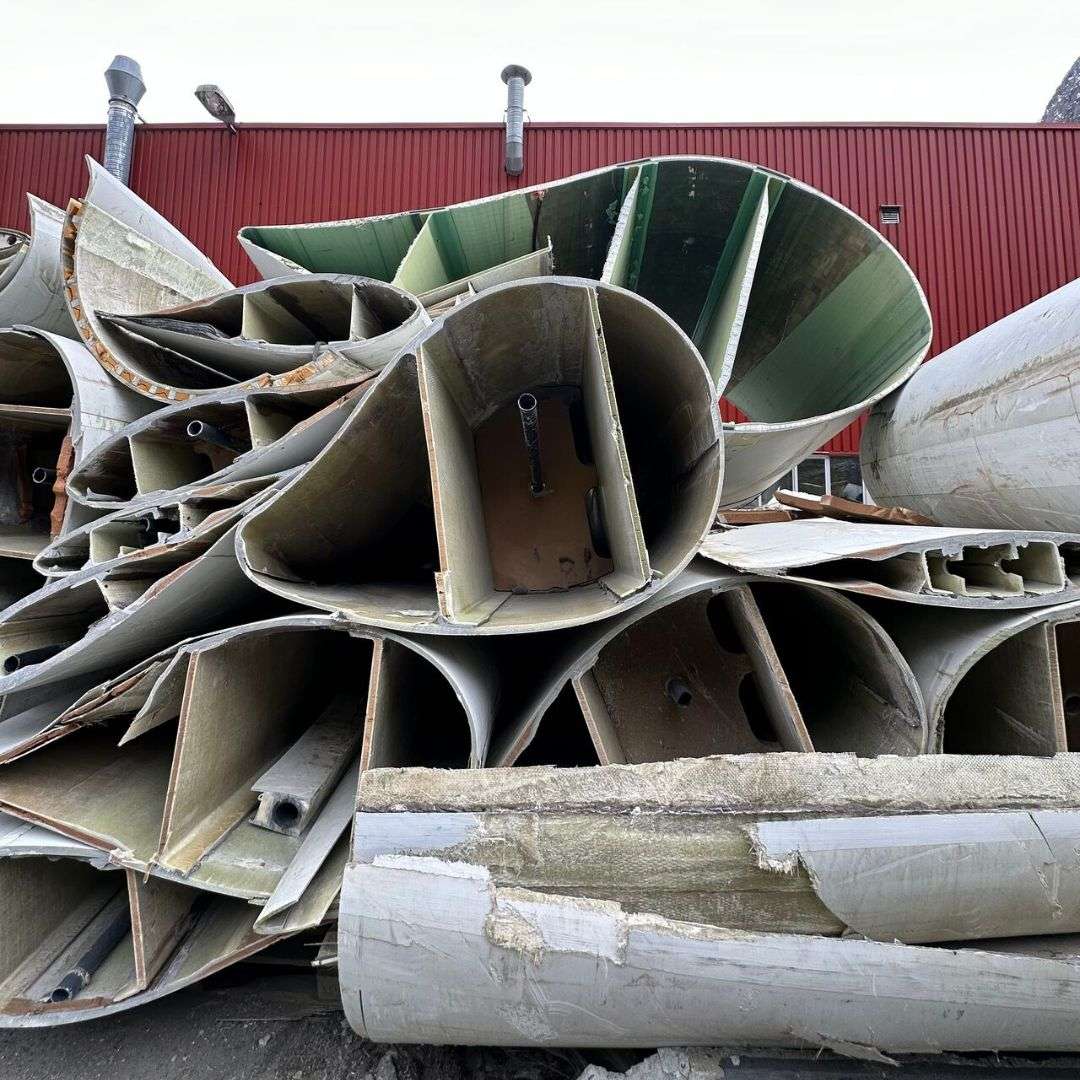
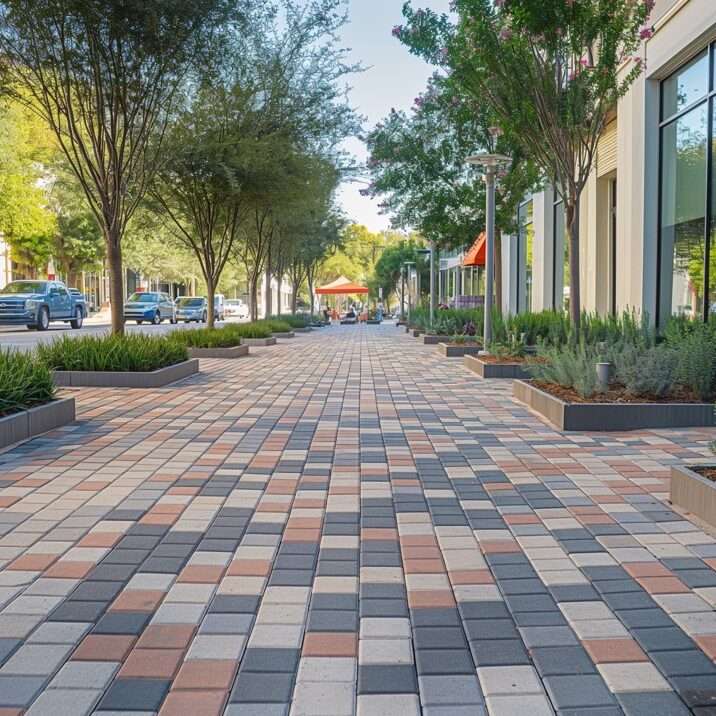
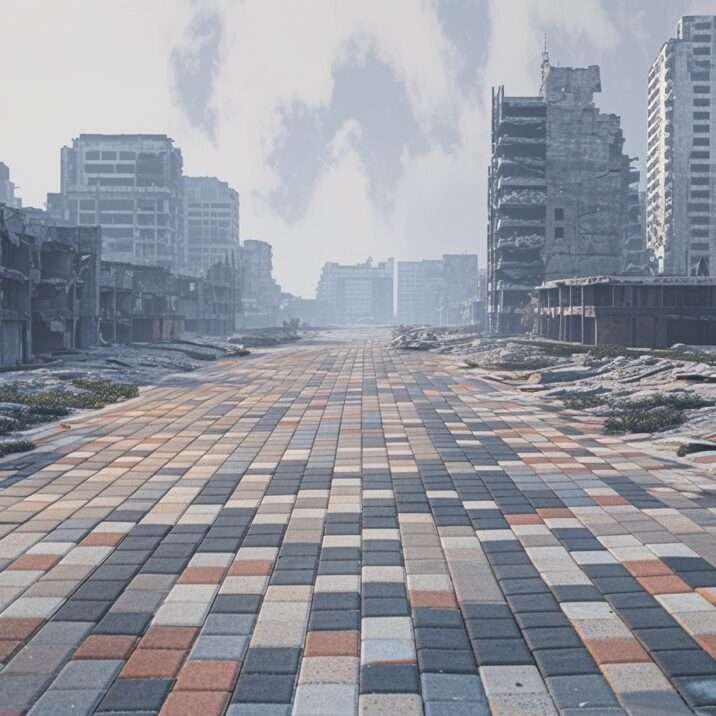
2. We make building materials that last.
We are very careful when choosing materials and designing products, so every one of them not only meets but also goes above and beyond industry standards. We promise you that our products will stand the test of time, and we give you a warranty to back it up.
3. Our products need minimal maintenance.
We design our building materials to last decades while being virtually maintenance-free. This ensures that we reduce the product’s lifetime costs, reduce its environmental impact, and, most importantly, save you time.
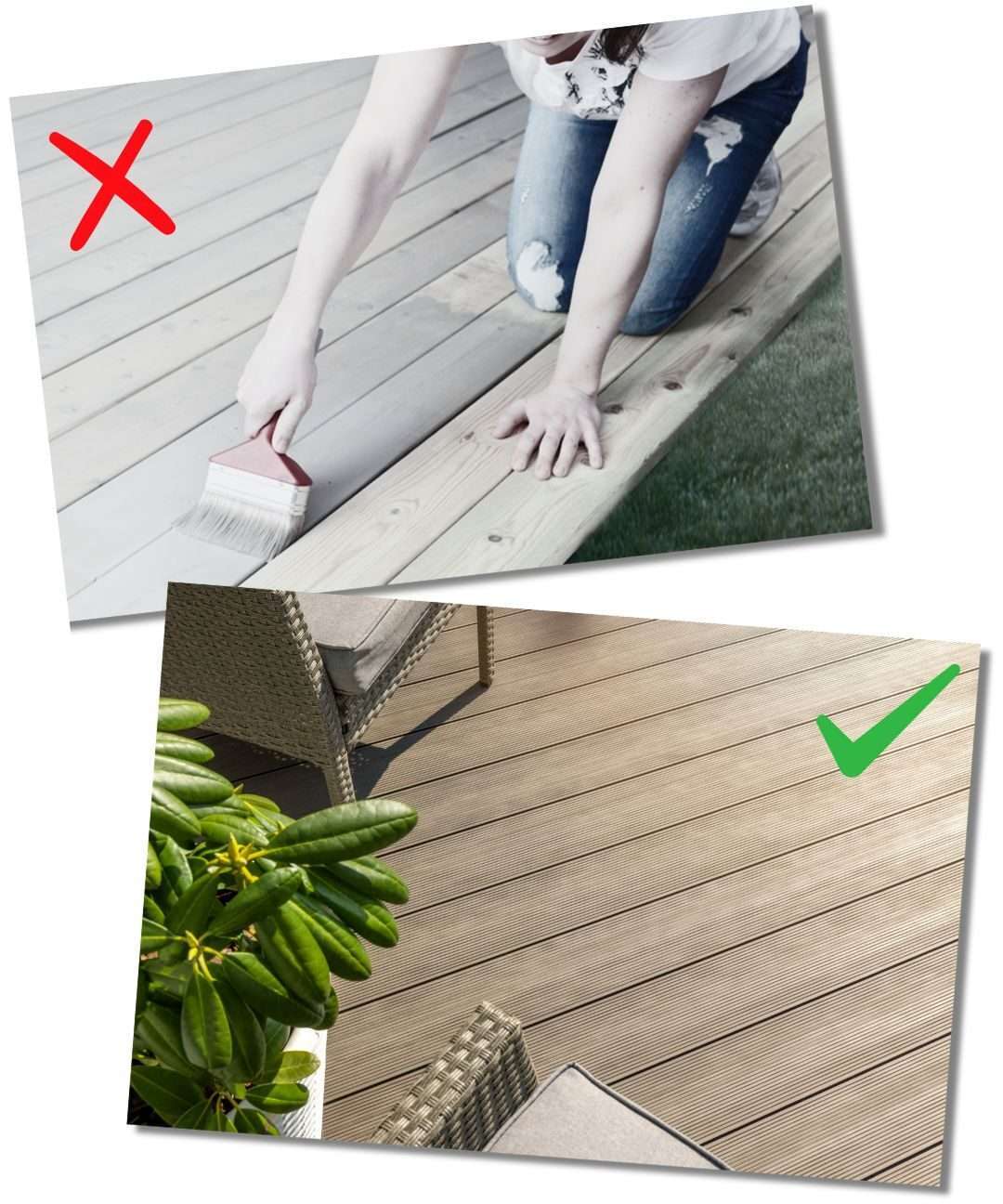
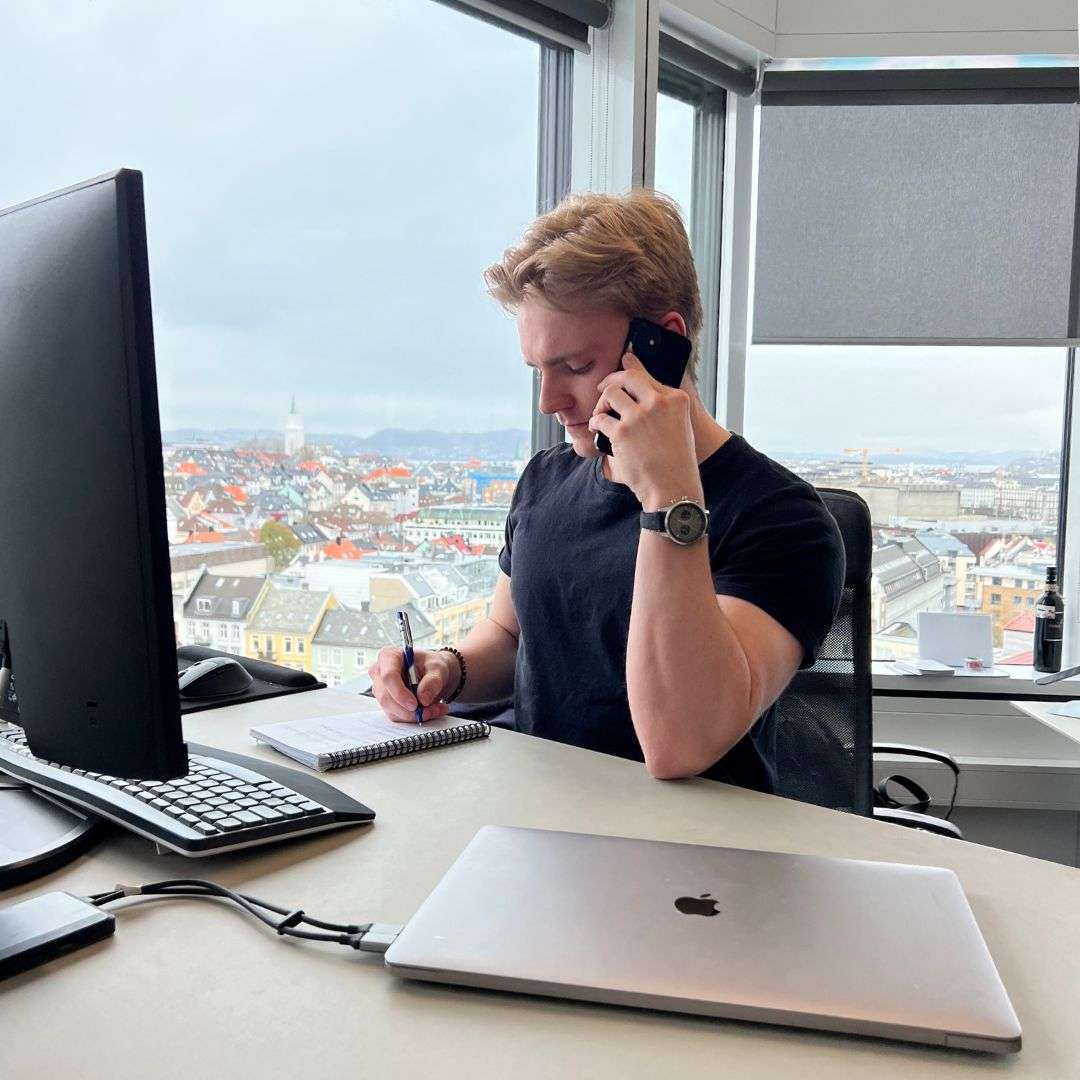
4. We only make what you want.
Your feedback helps us design products that you actually need and want to buy. We don’t believe in producing blindly, as that causes a huge risk of unwanted goods. We make sure that every composite panel, roof tile, and paver has a place by closely matching production to demand. The effect? Less waste and more utility.
5. We use the "pilot" model.
We start by making a prototype of every product and testing it thoroughly with experts in the field. Then, we give a small batch to the public to see if you’re interested. Because of this careful process, we don’t make too much, and if a product does well, we confidently make more of it to meet your needs.
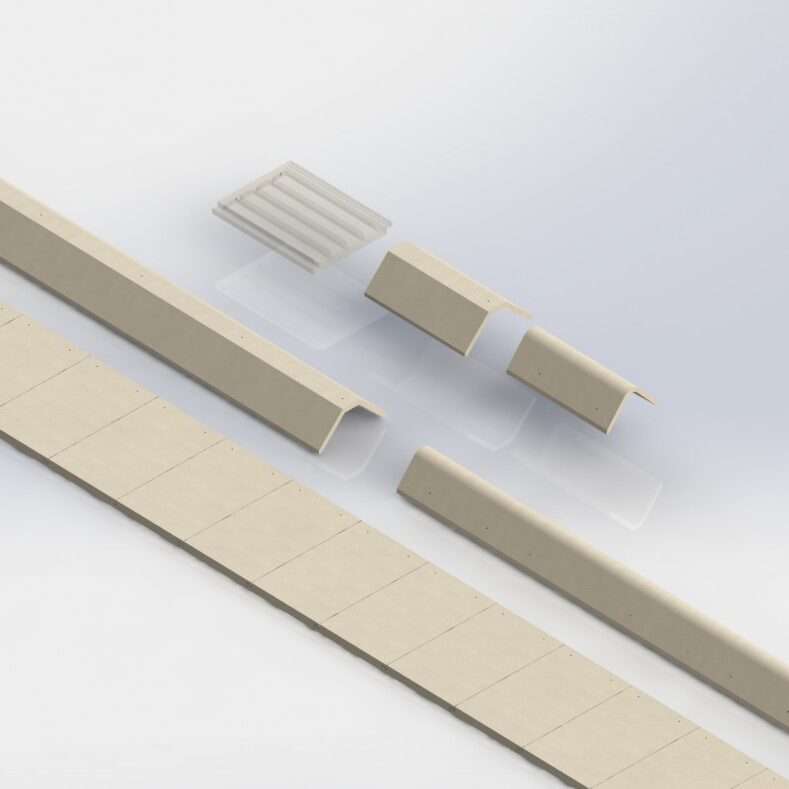
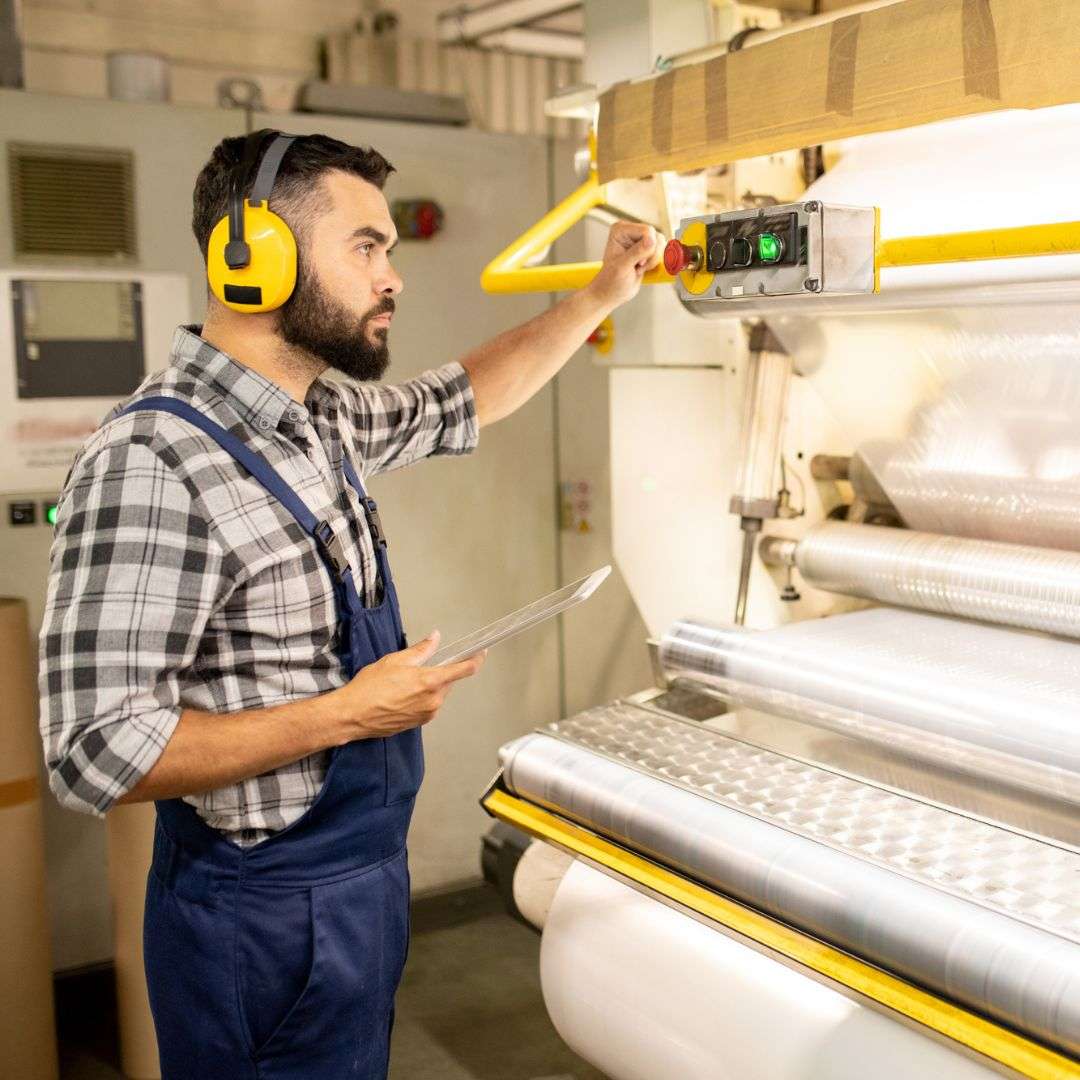
6. We produce on-demand.
At Bú Composite, we make our products only when an order is placed. This on-demand production model enables us to provide the lowest possible prices by reducing unnecessary storage and transportation. By streamlining our operations, we not only save money but also reduce our environmental impact, ensuring that every piece we create has a purpose and a place.
Thank you for reading all the way to the end.
We will update this page as we discover new ways to reduce waste and improve efficiency in our business.